Блоки из цемента своими руками
Технология изготовления опилкобетона своими руками
Многочисленные исследования специалистов, которые работают в сфере строительства, доказали, что опилкобетон является отличным материалом для возведения прочных и тёплых стен. Помимо этого, он отличается высокими теплоизоляционными свойствами, хорошими санитарно-гигиеническими показателями и огнестойкостью. Изготовить качественный опилкобетон своими руками не так уж и сложно, главное, придерживаться правильной пропорции и технологии производства.
Краткое описание материала
Опилкобетон относится к категории лёгких материалов. Это связано с тем, что для его изготовления используются обычные древесные опилки, песок и цемент. Впервые этот материал был разработан ещё в 1960 году, но своё применение получил только вначале 90-х. Засчет того, что опилкобетон обладает высокими санитарно-гигиеническими показателями, он широко используется для возведения различных зданий и учреждений. Блоки получаются очень крепкими, благодаря чему их можно смело подвергать любым механическим обработкам. Можно не бояться, что на опилкобетоне образуются трещины или сколы.
Многие потребители часто путают этот материал со специфическими арболитовыми блоками. Но между ними есть главное отличие — в них используются совершенно разные заполнители. Стоит отметить, что для арболита применяется специальная дроблёная щепка, которую получают в результате тщательного измельчения древесины. В состав также входят дроблёные стебли хлопчатника и камыша. А вот что касается опилкобетона, то для его изготовления нужен только опилковый заполнитель.
Особенности изготовления
Специалисты всегда акцентируют внимание на том, что для производства опилкобетона необходимо использовать только качественные опилки тех пород дерева, которые отличаются минимальным содержанием сахаров. Оптимальными в этом случае считаются:
Несмотря на то что лиственница отличается высокими прочностными характеристиками, она находится на самом последнем месте по популярности, так как в ней содержится высокий процент сахаров. К примеру, у ели начало набора прочности начинается через 14 дней после полного высыхания, а вот окончание этой процедуры происходит на сороковой день после изготовления. Что же касается лиственницы, то этот период длится гораздо дольше — более 30 дней для набора прочности и 140 дней для его окончания.
Чтобы добиться желаемого результата, все работы по опилкобетону нужно проводить в середине весны, чтобы к приходу осени все было готово. Из-за того, что из опилок выделяется специфический сахар, работать с ними нужно исключительно на свежем воздухе. Не стоит забывать о том, что опилки обязательно нужно полить чистой водой, чтобы смыть все имеющиеся остатки распада сахара.
Состав смеси
Именно от того, насколько правильно подобран каждый компонент, зависит качество будущего материала. Используемые блоки должны быть прочными и долговечными. Вне зависимости от марки опилкобетона, в его состав должны входить следующие компоненты:
Разница в пропорции зависит только от соотношения компонентов смеси. Строители отмечают, что блоки с большим содержанием цемента больше всего подходят для возведения многоуровневых нежилых зданий. Такая тенденция объясняется тем, что меняется коэффициент теплопроводности материала, а это чревато большими расходами на отопление. Если мастер решит использовать цемент М10, то коэффициент будет равен 0.21, что очень хорошо при любых условиях.
Для марки цемента М15 этот показатель составляет 0.24, что обусловлено незначительными изменениями в требованиях к прочности. Именно поэтому мастеру потребуется гораздо больше цемента, чтобы построить качественный двухэтажный дом. Что касается марки цемента М25, то его коэффициент увеличивается до 0.39, а это уже в два раза больше, нежели у блока М10. Конечно, такой опилкобетон получается более холодным, но он отлично подходит для возведения больших зданий.
Преимущества и недостатки
Каждый специалист знает, что перед тем использованием любого материала необходимо ознакомиться со всеми его плюсами и минусами. Помимо этого, чтобы изготовить строительные блоки из опилок своими руками, нужно учесть каждый нюанс. Начинать знакомство с опилкобетоном лучше всего с его сильных сторон.
Преимущества:
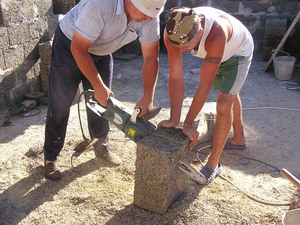
Среди недостатков можно выделить:
Блоки подвержены усадке.
- Очень часто геометрия материала оставляет желать лучшего.
- Достаточная гигроскопичность. Опилки хорошо впитывают влагу. Но важно отметить, что этот показатель не считается высоким среди стеновых зданий.
- Нужно много времени, чтобы опилкобетон достиг необходимой марочной прочности. В некоторых случаях это может занять несколько месяцев.
- В связи с тем, что технология изготовления блоков не является сложной, их часто изготавливают в кустарных условиях. Конечно, качество таких изделий не контролируется и не тестируется, что повышает риски покупки материала сомнительного качества.
Этапы самостоятельного производства
Чтобы изготовить качественные опилкоблоки своими руками, нужно придерживаться нескольких рекомендаций, которые были разработаны опытными специалистами. Это связано с тем, что только точное выполнение всех норм позволит получить качественное изделие, которое будет обладать необходимыми прочностными и эксплуатационными характеристиками. Основной алгоритм производства выглядит следующим образом:
На первом этапе осуществляется подготовка всех необходимых материалов. Стоит отметить, что нет необходимости приобретать основные составляющие компоненты заранее. Все это можно сделать непосредственно перед изготовлением блоков. В этом случае отлично подойдёт не только специализированный строительный магазин или склад, можно воспользоваться производственными отходами деревообрабатывающих предприятий.
- Все компоненты должны быть смешаны в одной ёмкости в соответствии с пропорцией. Для перемешивания может быть задействован механический способ с применением мощного бетоносмесителя либо ручным путём при помощи обычных лопат. Как показывает практика, автоматизация технологического процесса с помощью строительной бетономешалки позволяет существенно повысить итоговую производительность, а также улучшить качество продукции. В этом случае обеспечивается тщательно смешивание всех ингредиентов, которое помогает избежать последующего брака.
- На следующем этапе осуществляется формировка блоков. Огромным преимуществом обладает групповой процесс формировки. Эта технология подразумевает то, что тщательно перемешанный состав заливается сразу в несколько форм. В зависимости от масштабов стройки, специалисты могут использовать как единичные, так и групповые формы разборной конструкции. Они могут быть изготовлены из качественной древесины толщиной 2 см и обиты пластиком или же металлом. Использование обычной полиэтиленовой плёнки упрощает извлечение готовых блоков.
- На финальном этапе проводится сушка готового материала под открытым небом. Через 5 суток после заливки осуществляется снятие форм. В этом случае мастер должен ослабить затяжки барашковых гаек, извлечь резьбовые шпильки и поэтапно разобрать формировочный ящик. Длительность естественной сушки зависит исключительно от породы древесины (не более трёх месяцев). В течение этого промежутка времени существенно снижается количество влаги, и блоки приобретают необходимую эксплуатационную прочность.
Необходимые инструменты и формы
Не только опытные строители, но и начинающие мастера все чаще решают сделать опилкобетон своими руками. Технология изготовления подразумевает наличие щитков для опалубки. Они должны быть правильно вымерены, чтобы блоки получились максимально ровными. Желательно, чтобы доски для щитка имели толщину 38 мм. Опилки обязательно просеивают от накопившегося мусора и камней. Когда щепа и кора отсортированы, нужно добавить к ним подготовленную древесную стружку. Так можно увеличить итоговую прочность материала в несколько раз.
Укладка раствора может осуществляться в два типа форм:
Небольшие блоки. Такие формы имеют компактные размеры, и за один раз можно изготовить до 9 опилкоблоков.
- Габаритные блоки. Для такого материала необходимо подготовить вместительные ящики из досок. Стоит отметить, что чаще всего они разборные, так как это ускоряет процесс изъятия готового материала.
Специалисты утверждают, что к укладке приготовленного раствора необходимо приступать сразу, так как уже через несколько часов он начнёт застывать. Нужно помнить, что перед использованием внутренние части опалубки обязательно увлажняются обычной водой.
Укладывать раствор необходимо аккуратными слоями по 150 мм. При этом каждая часть должна быть тщательно утрамбована, так как это предотвращает образование пустот.
Через четыре дня опалубку необходимо аккуратно снять (но только в том случае, если раствор полностью застыл). А вот опилкоблоки желательно оставить досыхать ещё на четыре дня. Это делается для того, чтобы повысить итоговую прочность материала. Отдельно стоит учесть, что для сушки изготавливаемых блоков лучше всего использовать тот участок, где есть сквозняки, чтобы раствор застывал равномерно. Между каждым опилкоблоком должен присутствовать зазор. Если собирается дождь, тогда материал нужно укрыть плёнкой, чтобы предотвратить намокание.
Для гарантированной сушки должны быть задействованы столбы. Блоки можно уложить на кирпичи. Благодаря таким манипуляциям, можно добиться 90% прочности уже после месяца такой сушки.
Оптимальные пропорции
Как показывает практика, несоблюдение минимальных требований чревато негативными последствиями, которые могут существенно снизить качество возведённого здания. Пропорции зависят от того, какую марку цемента будет использовать мастер. Оптимальное соотношение компонентов выглядит следующим образом:
Для цемента марки М10 нужно: полное ведро чистого песка, 5 кг цемента и три полных ведра опилок.
- Опилкобетон на основе цемента М15: 1.5 ведра песка, полведра цемента и 4 ведра древесных опилок.
- Цемент М25: 1.5 ведра песка, 0.5 ведра цемента и три ведёрка опилок.
Стоит отметить, что каждый мастер должен придерживаться именно этой рецептуры, так как это было проверено в течение нескольких десятилетий. Строителей не должно смущать отсутствие прогрессии в пропорциях и количестве. Такая тенденция связана с тем, что в каждом случае компоненты работают совершенно по-разному. Что касается гашёной извести, то она нужна для надёжного обессахаривания опилок.
Как зарабатывать, изготавливая строительные блоки
Зачем делать блоки?
Что необходимо иметь для этого?
Из чего творить блоки?
Как их производить?
Почему выгодно самому творить блоки?
Какова прибыль от этого?
С чего начать и как развивать этот бизнес?
В этой статье Вы получите ответы на все поставленные вопросы и сможете «включить» для Себя надежный и, зависящий только от Вас, источник дохода.
И так, разберемся по порядку.
Зачем делать строительные блоки?
Вы, наверняка, обратили внимание, что последние 4-5 лет бурно идет строительство. Строят от мелких и средних частных построек: гаражей, дач, усадеб, мастерских, цехов, с/х строений, до крупных производственных, жилых зданий, хранилищ, центров. Специалисты строительных специальностей востребованы как никогда ранее.
Появляются новые строительные технологии и материалы. Но всегда ли они доступны по цене и технологии широкому кругу застройщиков?
Поэтому они мало применяются в малом и среднем строительстве, как в крупных городах, так и в малых поселках.
Наиболее доступным строительным материалом остается так называемый шлакоблок и кирпич.
Причем кирпич часто уступает шлакоблоку по цене, теплопроводности и простоте кладки.
А вот пустотные строительные блоки удобны и доступны большинству частным застройщикам.
Да потому, что благодаря своим свойствам:
— из них просто построить малоэтажное (2-3 этажа) строение (гараж, дом, дачу, хозблок, мастерскую и т.п.) даже не прибегая к услугам каменщика. (1 блок = 3-4 кирпича);
— стены из шлакоблоков звуко- и тепло- не проницаемы;
— цена шлакоблока ниже цен на кирпич, пеноблок и других строительных материалов из-за дешевизны и доступности его компонентов (см. ниже);
— только шлакоблок можно изготавливать самому. Еще саман (глиняно-соломенный кирпич) тоже можно делать самостоятельно.
Так как же производить шлакоблоки самому?
Что необходимо для производства строительных блоков?
Известно, что шлакоблок производили ЖБК на специальном оборудовании с использованием пропарочной камеры. Поэтому производство качественного блока в бытовых условиях было не доступно.
Но если есть спрос, значит неотвратимо и предложение. И оно есть!
С 1994 года опыт производства строительных блоков в частном хозяйстве и на малом производстве дал ответ на поставленный вопрос.
Что для этого необходимо?
Уточним подробнее каждый пункт.
Вибростанок
Есть разные конструкции вибростанков. В бытовых условиях производства и малом бизнесе уверенно зарекомендовал себя в странах СНГ ручной, электрический, малогабаритный шлакоблочный вибростанок МЗ30 (выпускается 14-й год). В народе известный как «Мечта застройщика»
Сырьё
Для производства строительных блоков необходимы следующие компоненты:
- — цемент
- — наполнитель
- — пластифицирующая добавка (желательна, но не обязательна)
- — вода (без комментариев)
Цемент – портландцемент марки 400. Допустим и другой. Но необходим подбор пропорций. Например, при использовании цемента марки 300, его расход следует увеличить на 10-15%.
Наполнителями для бетона могут быть самые разные материалы: песок, щебень, шлак, граншлак, зола, опилки, стружка, отсев, керамзит, гипс, лом кирпича и другие природные и производственные материалы.
В зависимости от местных условий, требований к производимым блокам и себестоимости можно выбирать соответствующий наполнитель. Перечислю несколько популярных составов бетона и основные группы бетонов
1). Шлак с металлургических предприятий (серого или темно серого цвета с высоким содержанием цемента, сеянная мелкая фракция) – 9 частей
+ цемент – 1 часть
+ вода 0,5 объема цемента
2). Граншлак с металлургических предприятий (желто-зеленоватого цвета с высоким содержанием цемента, сеянная мелкая фракция) – 4 части
+ мелкий отсев – 4 части
+ цемент – 1 часть
+ вода 0,5 объема цемента
3). Другие шлакобетоны
4). Бетоны на песке и щебне
5). Бетон на отходах кирпича
и другие бетоны с разным сочетанием перечисленных.
Теперь понятно, что бытующее название «шлакоблок» не самое точное определение возможных строительных блоков.
Пластифицирующая добавка – это не обязательный компонент бетона. Но ее присутствие обеспечивает: раннюю прочность блоков (это очень важно при ограниченных производственных площадях), повышает качество блоков (снижается трещинообразование и истираемость блоков), улучшается водонепроницаемость и морозостойкость бетона.
Количество добавки очень незначительно – порядка 5г на блок.
Технология изготовления строительных блоков:
- Подготовка бетона
- Производство блоков
- Просушка и складирование готовых блоков.
Подготовка бетона (на примере ранее приведенного 2-го рецепта бетона)
1). Засыпаете 4 лопаты мелкого отсева + 4 лопаты гранулированного шлака
2). Засыпаете 1 лопату цемента
3). Тщательно перемешиваете
4). Добавляет в 7-9 л воды + 250 мл (половину пол-литровой банки) растворенной УПД. Раствор добавки готовится так: в 40 литровую емкость высыпают 0,5кг УПД и тщательно перемешиваете до полного растворения.
5). Перемешиваете. При этом бетон качественно пропитывается раствором УПД.
Производство блоков
1). Засыпаете в вибростанок готовый бетон с небольшой горкой. Кратковременно, на 1-2 сек. включает вибратор – бетон садится, мастерком, в одно движение, разравниваете поверхность чуть осевшего бетона.
2). Устанавливаете прижим и, без особого усилия, давите на него, включив вибратор.
Блоки с круглыми и прямоугольными пустотами вибрируются 4-5 сек. до опускания прижима на ограничители.
Узкие полные блоки (2шт.) вибрируются 5-7 сек.
3). С вибрацией поднимаете станок — блок остается на площадке.
Просушка и складирование готовых блоков
При использовании УПД готовые блоки можно убирать с площадки и складировать уже через 5-6 часов. Без УПД – через двое суток.
После этого времени блоки не рассыпаются при соблюдении пропорций бетона и технологии их изготовления.
Складировать готовые блоки советую в пирамидальные штабели в один блок с небольшим (2-3см) просветом между блоками – для дальнейшего досыхания боковых граней.
В каждой такой пирамиде по 100 штук. Легко считать. Каждую пирамиду полезно промаркировать датой и временем изготовления последнего блока. Это пригодится при реализации. На 4-й, 5-й день можно отгружать.
Производственная площадка
- Помещение с ровным бетонным полом.
Можно производить блоки круглый год. Желательна хорошая вентиляция и отопление в холодное время.
- Открытая ровная площадка.
Может быть бетонная или земляная, покрытая полиэтиленовой пленкой для сохранения товарного вида блоков (не пачкается тыльная грань).
- Открытая, относительно ровная площадка без предварительной подготовки.
На такую площадку можно выкладывать готовые блоки на поддончиках.
С чего начать производство строительных блоков?
1. Выберите оптимальный местный материал для бетона, учитывая его стоимость и доставку.
2. Рассчитайте себестоимость 1 блока с учетом компонентов бетона.
3. Определитесь с производственной площадкой.
4. Приобретите вибростанок.
5. Освойте приведенные технологии.
На первых порах бетон можно готовить вручную. В последствии эффективнее и легче – на электрической бетономешалке объемом 0,2-0,5куб.м (лучше 0,5 с учетом перпективы).
Почему выгодно самому творить строительные блоки?
Приведу мои реальные затраты на заполнитель с доставкой и цемент, расчет себестоимости изготовления блоков и окупаемости вибростанка «Мечта застройщика» по производству шлакоблока в г.Запорожье (Украина) в 2004 году на примере бетона из граншлака (серого) и цемента.
Исходные данные:
8 куб.м шлака – 30 долларов/машина с доставкой по городу (КРАЗ или большой МАЗ)
Цемент:
Пропорция 1:9 – 0,88 куб.м или 18 мешков по 3 доллара = 54 доллара
Цена вибростанка – 200 долларов
Общий объем раствора:
Пропорция 1:9 – 8 + 0,88 = 8,88 (куб.м)
Объем раствора на 1 ГОСТовский шлакоблок:
— общий объем: 39см х 19см х 19см = 0,014 (куб.м)
— при d = 9,5 см: 3 х 3,14 х 4,75**2 х 15 = 3188 куб.см = 0,003188 куб.м
— объем раствора на 1 ш/блок при d = 9,5 см: 0,011 куб.м
Таблица результатов расчета:
Диаметр пустот (см)
Кол-во ш/блоков с объема раствора (шт.)
Себестоимость 1 ш/блока (дол.) 84/830=0,1
Кол-во ш/блоков для окупаемости станка (шт.) розничная цена 1ш/блока = 0,3 дол. 200/0,3=667
Время окупаемости (дней) с учетом 400 ш/блоков в день
Расчет доходности и прибыли:
Принимаем исходные допущения:
Наименование
Диапазон значений
Опорное значение
Время формирования 1 блока (сек.) без УПД
Количество блоков в 1 час, учитывая время загрузки бетона в МЗ30 сек. (штук)
Количество блоков в 1 день (8 часов) штук
Розничная цена 1 шлакоблока (в 2005 году): на Украине
_______________ 2,0грн. (0,4 $)
Доходность (Из предыдущей таблицы следует, что себестоимость 1 ш/блока составляет 1/3 от его розничной цены)
В день произвести блоков на сумму:
За месяц произвести блоков на сумму:
Прибыль составит:
2347 $
2933 $
- Если применить УПД, то производительность существенно возрастет.
- Рекорд принадлежит Виктору Романову и Сергею Рахманинову, которые за день изготовили 700 блоков 390*138*188 в июле 1998г
Развитие и расширение бизнеса
1. Нанимать ответственных работников, достойно их заинтересовав. (У нас в городе – 20коп. (0,04цента) за блок, в районе – 0,02цента.)
2. Начиная реализацию, снижать розничную цену, тем самым составив достойную конкуренцию и получив благодарных клиентов и их рекомендации. (Важно! Качество должно быть непременно достойным).
3. В теплый сезон или в отапливаемом помещении (вне зависимости от сезона), можно организовать работу и в 2 смены.
4. При этом предприниматель зависит только : от наличия напряжения в сети и от здоровья 1 рабочей силы (на первом этапе, до окупаемости, можно и самому поработать со станком).
5. Если целесообразно, сдавать станок в аренду «застройщикам».
6. Выполнять заказы «застройщиков» прямо на их площадке, сэкономив им деньги на погрузку, перевозку и разгрузку блоков.
7. Кроме того, – Вам не потребуется разрешения Госэлектронадзора, так как всё оборудование рассчитано на обычную бытовую сеть!
Постановлениями Правительства РФ от 13.08.97 № 1013, Госстандарта РФ № 86 от 08.10.2001 г. и Госстроя РФ № 128 от 24.12.2001 г. в перечень продукции, требующей обязательной сертификации не входят строительные бетонные блоки с различными наполнителями (шлак, керамзит, опил и т. п.), а так же виброформовочное оборудование для их производства.
Таким образом, бизнес по производству строительных блоков можно развивать поэтапно:
- Начать с минимальных затрат на приобретение вибростанка, 1 машины местного сырья в качестве наполнителя бетона, 15-20 мешков цемента.
Дать бесплатные объявления о реализации качественного щлакоблока.
Произвести 800-1000 блоков. Быстро из реализовать, снизив розничную цену.
- Приобрести бетономешалку и следующую партию сырья + УПД.
Выровнять цену до розничной (по желанию).
Дать бесплатные объявления + платное.
- Производительно, с наработанным опытом производства, изготавливать качественные блоки, успевая выполнять заказы.
Объявления давать уже не нужно: высокое качество блоков + реклама «из уст в уши» сделают свое дело.
Организовать 2-х сменное производство строительных блоков.
Расширить номенклатуру производимых блоков.
Приобрести дополнительные вибростанки, возможно, и бетономешалку.
Набрать работящих работников
Успевать тратить прибыль или вложить ее в новый бизнес, столь же рентабельный.
Чего я Вам искренне желаю!
Успехов и Процветания!!
Виктор Смольников — автор проекта
«Каталог полных бизнес-пакетов» masterdela.info
mailto:svs7@pochta.ru,
Украина, г.Запорожье, август 2005 года
*Статье более 8 лет. Может содержать устаревшие данные
Самостоятельное изготовление блоков: инструкция и советы
Строительство зданий из блоков намного быстрее, чем из кирпича. В строительных магазинах много разновидностей такого материала, но для экономии средств можно легко сделать такие блоки для строительства самостоятельно.
Купить блоки или сделать самостоятельно?
Строительные блоки используют не только для строительства стен. В продаже можно найти блоки различной твердости и качества. Блоки, приобретённые в специализированных магазинах, являются стандартных форм. Материал, сделанный своими руками можно подстраивать под нужные размеры.
Использовать можно различные материалы для блоков строительных. Плюсом изготовления строительных блоков самостоятельно является дешевая себестоимость материала.
Самодельные блоки
Для изготовления самодельных блоков необходимо определится с будущими размерами блоков. Самый простой вариант изготовление блоков это использование специальных форм.
Самодельные блоки можно изготавливать различных форм, что позволяет использовать блоки не только строения стен, но и для отделочных работ.
Форма для изготовления блоков
Металлические
В продаже есть готовые формы для изготовления блоков, они имеют стандартные размеры. Можно сделать формы самостоятельно для этого необходимо подготовить следующие материалы и инструменты:
- Инструмент УШМ (для резки метала)
- Аппарат сварочный
- Крупнозернистая наждачная бумага
- Дрель по металлу
- Метал толщиной 5 мм
- Метал толщиной 3 мм
На металлическом листе 5 мм сделать разметку необходимого размера, например 260 мм и 196 мм. Должно получиться четыре детали.
Пусто образователи необходимы для:
- Экономии раствора
- Снижения теплопроводности стен
Для формы необходимо три пусто образователя. Необходимо сделать три заготовки подходящего размера и свернуть их в цилиндры и проварить с внутренней стороны.
Необходимо взять полоску метала шириной 30-40 мм для крепления пусто образователей между собой. В верхней части пусто образователей делаются пропилы, с помощью которых цилиндры привариваются к металлической полоске.
Формы из дерева
Формы для изготовления блоков могут быть сделаны из дерева. Для экономии времени для изготовления блоков, можно сделать форму большую с отдельными ячейками.
Для удобного вынимания готового блока из форм, необходимо внутреннюю поверхность формы окрасить масляной краской.
Используемый материал для изготовления блоков
Большой плюс блоков изготовленных своими руками это широкий выбор материала
В зависимости от материала можно выделить несколько видов блоков:
- Блоки шлакобетонные
- Блоки с использованием жидкого стекла
- Саманные блоки
- Стружкобетонные или арбалитовые блоки
В качестве наполнителя в строительных блоках можно использовать:
- Золу
- Шлак
- Отсев
- Щебень
- Гипс
- Опилки древесные
- Солому
- Битый использованный кирпич
Какое потребуется оборудование?
Для начала изготовления блоков необходимо подготовить следующие инструменты:
- Форма для изготовления блоков
- Вода для смачивания форм
- Вибрационная плита ( необходимо для уплотнения раствора)
- Шпатель для разравнивания раствора
- Мастерок
- Совковая лопата
- Ведра
- Емкость для перемешивания раствора
- Металлическая или резиновая ровная пластина ( для сушки готового изделия)
- Необходимые компоненты для раствора
Виды блоков
- Шлакоблок – в качестве наполнителя для блоков используется шлак. Такие блоки огнеустойчивы и устойчивы к низкой температуре.
- Опилкобетон – удобны при укладке. Очень просты в применении имеют легкий вес.
- Блоки с использованием гравия – имеют большой вес, трудны в укладке
- Блоки керамезитные – обладают отличными теплоизолирующими свойствами. Имеют легкий вес и хорошую крепость.
- Блоки, содержащие древесные опилки камень и различные отходы.
Чтобы ускорить процесс производства необходимо изготовлять несколько форм. Для изготовления блоков необходимо:
- Подготовить формы для изготовления блоков
- Установить на гладкую ровную поверхность ( металлический или прорезиненный лист )
- Приготовить раствор с необходимым наполнителем
- Смачивать форму водой либо машинным маслом ( для легкого извлечения)
- Накладывается раствор в подготовленную форму
- Необходимо включить виброплатформу на 2-4 минуты для уплотнения раствора и выхода лишнего воздуха и воды.
- Необходимо шпателем выровнять поверхность блока
- Переместить форму в место сушки .для этого можно использовать открутую площадь с навесом
- Через минут 30-40 снять формы с готовых блоков.
- Оставить блоки на 2-3 суток в месте сушки. После переместить в сухое место на 20-25 дней. По истечении этого срока блоки готовы к использованию.
Изготовление керамезированных блоков
Керамизированые блоки – это блоки, состоящие из наполнителя керамзит.
Для изготовления раствора необходимо:
- 1 часть цемента
- Пять частей наполнителя керамзит
- Песок просеянный – 3 части
- 1 часть вода
Необходимо замешать раствор и изготовить блоки по следующей инструкции:
- В смазанные формы накладывается раствор
- Утрамбовывается
- Через 15-20 минут снять формы
- Оставить изделие на ровной поверхности. По истечении 12-13 часов переносятся в любое место защищённое от дождя .
- Через 20 дней блоки готовы к строительству.
Преимущества такого вида строительного материала:
- Блоки имеют маленький вес
- Устойчивы к низким температурам
- Влагоустойчивы
- Высокая прочность
- Невысокая себестоимость
Изготовление блоков из бетона
Процесс изготовления блоков из бетона можно разделить на несколько последовательных этапа:
- Подготовка форм для изготовления блоков. Вначале формы следует смочить водой , это предотвратит налипание на внутренних стенках раствора
- Заполнить формы раствором и установит на вибрационную платформу , для усадки раствора на несколько минут
- После того как раствор закрепнет можно снимать формы
Ингредиенты раствора:
- Цемент -1 часть
- Песок – 4 часть
- Гравий мелкий – 4 часть
- Известь – 4 часть
- Вода – до получения средней густоты
Бетонные блоки получают свою прочность по истечении 28 дней.
Изготовление опилкобетоных блоков
Перед приготовлением блоков необходимо материалы:
- Цемент
- Песок мелкой фракции
- Известь не гашенная
- Опилки
Для приготовления раствора необходимо:
- Просеять опилки
- Смешать цемент, песок и известь
- Добавить опилки и снова перемешать
- Добавить воду до средней густоты
- Добавить хлорид кальция для улучшения клейкости компонентов
Изготовление блоков:
- Форму необходимо выстелить полиэтиленовой пленкой
- Наложить раствор
- Утрамбовать любым удобным способом
- Оставить формы для застывания на 4-6 дней
- Достать из форм и сушить еще два месяца
Изготовление саманных блоков
Для изготовления саманных блоков для строения необходимо:
Точного соотношения нет, обычно раствор оценивается визуально. Самый оптимальный вариант:
- Глина – 1 куб.м
- Солома – 20 кг.
- Песок – 25-30 %
Для изготовления блоков следует выполнить такие действия:
- Приготовить солнечную ровную площадку
- Сделать раствор
- Заполнить формы раствором
- Уплотнить
- Убрать шпателем лишний раствор
- Через 20-30- минут формы следует снять
Блоки сохнут 10 -15 дней. Главное условие не допускать попадания воды. Какой бы метод изготовления блоков не был выбран, в любом случае себестоимость изготовления таких строительных материалов будет ниже, чем приобретение готовых изделий. Блоки самостоятельного изготовления выходят намного экологичнее и есть выбор необходимых размеров.
Как сделать блоки из опилок (щепы, стружек) и цемента — технология изготовление кирпича
Блоки из опилок и цемента – легкий и прочный современный строительный материал, входящий в группу бетонных изделий с пониженным удельным весом. Опилкобетон производится из щепы разных пород древесины и цементного раствора, выступающего в роли вяжущего. Материал обладает уникальными свойствами, что делает его популярным для использования в самых разных сферах строительства.
Основные характеристики опилкобетона – высокие теплотехнические свойства, экологичность, повышенная прочность и стойкость к огню, хорошая паропроницаемость, сохранение свойств при резких перепадах температуры, высоком минусе и плюсе. Немаловажно и то, что стоимость блоков сравнительно невысокая и при желании их можно сделать своими руками.
Прежде, чем применять блоки из стружки и цемента в тех или иных работах, необходимо тщательно изучить их технические характеристики и выполнить расчеты. При желании самостоятельно производить материал обязательно нужно ознакомиться с технологией и правилами выбора сырья.
Блоки на основе стружки и цемента – область применения
Применяется материал в самых разных сферах, но в основном в возведении малоэтажных зданий. Чаще всего из опилкобетона строят дачи, гаражи, внутренние перегородки в частных домах, таун-хаусы, погреба, коттеджи, здания бытового использования.
Популярен опилкобетон и для проведения работ по утеплению подвальных помещений, капительных стен сооружений, создания изоляционного слоя. Могут пригодиться блоки при строительстве разного типа ограждений. Редко они используют там, где есть большие нагрузки – строительство фундамента, несущих стен, перекрытий и т.д.
Там, где отмечена повышенная влажность, плиты или блоки желательно выполнять с дополнительным слоем изоляции, так как они будут впитывать влагу. При должной защите и учете всех свойств опилкобетон из щепы способен долго сохранять геометрическую форму, а также механические и эксплуатационные свойства.
Преимущества и недостатки
Прежде, чем начинать изготовление блоков из опилок и цемента своими руками, нужно хорошо изучить свойства материала, плюсы и минусы. С учетом специфичности его состава опилкобетон подходит далеко не для всех работ и условий эксплуатации, но при выполнении всех требований может стать действительно удачным выбором.
Основные достоинства опилкобетона:
- Высокий уровень теплоизолцяии – дома хранят прохладу летом, тепло зимой, словно термос.
- Экологичность и безопасность для людей – отсутствие токсинов и вредных выделений гарантирует в жилье положительный микроклимат и отсутствие аллергий.
- Прочность – неплохие структурные показатели, некоторые виды опилкобетона можно использовать для возведения несущих конструкций (но не выше 3 этажей).
- Стойкость к огню – за счет введения в состав синтетических добавок, делающих материал способным в течение 2 часов не гореть при температуре +1200 градусов.
- Прекрасная паропроницаемость – за счет пористой структуры опилкобетон пропускает воздух, не задерживает влагу.
- Стойкость к резким перепадам температур – не боится замораживания/оттаивания, не деформируется при внешних воздействиях.
- Доступная стоимость – немного дороже газобетона, но при самостоятельном изготовлении цена еще понижается.
- Хорошие показатели звукоизоляции – благодаря пористости материала он работает в обе стороны (снаружи/внутри).
- Простая работа – легкий монтаж за счет минимального веса и идеальных геометрических параметров, распил, сверление с сохранением целостности структуры и формы.
- Использование вторсырья – все виды цементно-стружечных блоков и плит создаются на базе щепы или стружки, которые представляют собой отходы деревообработки. Купить опилки можно по небольшой цене.
- Длительный срок эксплуатации – при обеспечении оптимальных условий блоки из опилок и цемента служат десятилетия.
- Небольшой вес – что облегчает монтаж и снижает общее давление конструкции на основание.
Из недостатков материала стоит отметить такие, как: низкий уровень влагостойкости и необходимость в защите, ограниченный выбор сырья в плане пород древесины, большая длительность этапов производства (после того, как материал залит в формы, он должен затвердевать и сушиться минимум 3 месяца до начала работ).
Блоки из опилкобетона: характеристика
Опилкобетон предполагает определенные свойства и требования по использованию в строительстве. Так, для предотвращения попадания влаги обычно цоколь дома делают из бетона или кирпича высотой минимум 50 сантиметров от отмостки. Также вылет карнизов за границу фасадных стен делают минимум 50 сантиметров с установкой системы отведения талой, ливневой воды.
Толщина швов между блоками составляет около 10-15 миллиметров, нередко блоки используют лишь для кладки утепляющего внутреннего слоя.
Состав блоков
Основные компоненты опилкобетона:
- Песок – повышает прочность, но снижает свойства теплоизоляции (поэтому важно подобрать оптимальную пропорцию)
- Портландцемент – минимум марки М400
- Деревянная стружка (щепа) – усиливает звуко/теплоизоляцию, перед применением сушится
- Специальные добавки – для обеспечения огнестойкости, пропитки от грызунов и т.д.
Компоненты
В производстве опилкобетона могут использоваться отходы самых разных пород древесины: пихта, сосна, тополь, ель, бук, береза, ясень, граб, дуб, лиственница. Но лучшим выбором считается щепа хвойных деревьев, так как в ней повышена концентрация смолы, защищающей от гнили.
Для сосны характерно ускоренное твердение – блоки можно использовать в строительстве уже через 40 суток после заливки в формы. Дубовая щепа и лиственница продлевают срок набора прочности – они требуют отстаивания на протяжении минимум 100 суток.
С целью повышения прочности, стойкости к огню и понижения способности впитывать влагу древесные компоненты готовят специальным образом: вымачивают в известковом молоке, сушат (принудительно/естественно), замачивают в смешанном с водой жидком стекле (1 часть стекла и 7 частей воды). Для обеспечения однородности материала щепу пропускают сквозь сито с ячейками 10-20 миллиметров.
Пропорции
Соотношение материалов в составе напрямую влияет на плотность и другие характеристики. Опилкобетон бывает разных классов, которые определяют свойства и пропорции. Так, М5/10 классы используют для утепления и работ по реконструкции, М15/20 – для возведения внутренних/внешних стен.
Пропорции материалов для 1 м3 опилкобетона:
- 5 марка (плотность около 500 кг/м3) – по 50 кг цемента и песка, по 200 кг извести и опилок
- 10 марка (650 кг/м3) – 100 кг цемента, 200 кг песка, 150 кг извести и 200 кг опилок
- 15 марка (800 кг/м3) – 150 кг цемента, 350 кг песка, 100 кг извести и 200 кг опилок
- 20 марка (плотность 950 кг/м3) – 200 кг цемента, 500 кг песка, 50 кг извести, 200 кг опилок
Смешивание компонентов
Процесс смешивания такой: все материалы отмерить, смешать сухими песок и цемент, добавить известь и опилки, снова смешать тщательно, порционно вливать воду, добиваясь нужной консистенции раствора.
Размер опилок
Данный параметр мало влияет на прочность блоков, тут больше важна однородность материала, а не величина. Поэтому опилки выбирают такие, чтобы все компоненты были единого размера и дали возможность приготовить однородную смесь.
Подходит стружка с пилорамы – неважно, дисковой или ленточной. Но не стоит брать опилки с калибровочных или оцилиндровочных станков, так как они неоднородны по структуре.
Виды древесно-цементных материалов
Разнообразие древесно-цементных материалов не очень большое. Отличаются блоки по типу щепы и пропорциям материалов в составе, структуре, типу связующего. Самые популярные виды цементно-стружечных блоков: фибролит и арболит, цементно-стружечная плита, опилкобетон и ксилолит.
Арболит
Производится из большого объема древесной щепы, песка, портландцемента, воды и химических добавок. Обычно в работу идут отходы деревообработки хвойных и лиственных пород, реже – солома-сечка, конопляная/льняная костра, измельченный стеблями хлопчатник и т.д.
Арболит бывает теплоизоляционным и строительным. В первом виде больше щепы, второй – более прочный. Где применяется: напольные плиты, кирпич под выгонку внутренних/наружных стен, покрытия и перекрытия, крупные стеновые панели.
Фибролит
Обычно поставляется в формате плит из цемента и стружки. Для производства используется щепа длиной 35 сантиметров и больше, шириной до 10 сантиметров, которая размалывается до состояния шерсти.
Опилкобетон
Данный материал похож на арболит, но не так требователен к типу и параметрам щепы древесины. Состоит из цемента, песка, воды, опилок различной фракции, могут быть включены глина и известь. Пропорция песка тут может быть больше, чем в арболите, поэтому и прочность выше при идентичной плотности.
Основное преимущества опилкобетона – низкая стоимость при отсутствии особых условий по эксплуатации, что делает использование его в строительстве более выгодным.
Цементно-стружечные плиты
Материал создают из замешанной на цементе, воде и минеральных добавках древесно-стружечной смеси, которую потом дозируют, заливают в формы, прессуют и обрабатывают высокой температурой. Главные преимущества плит: негорючесть, стойкость к морозу, биологическая инертность.
Плиты нередко используют в сборных конструкциях, в реализации внутренних и фасадных работ. Плиты отличаются высоким уровнем влагостойкости, из недостатков можно выделить лишь достаточно большой вес и низкую эластичность. При изгибах плиты ломаются (при этой демонстрируют хорошую стойкость к продольным деформациям), поэтому применяются часто с целью усиления каркаса.
Ксилолит
Песочный материал, сделанный на базе магнезиального вяжущего и древесных отходов (мука и опилки). Также в состав вводят минеральные тонкодисперсные вещества: мраморную муку, тальк, щелочные пигменты и т.д. Производство осуществляется с применением температуры в +90 градусов и давления в районе 10 МПа, что делает материал особенно прочным после затвердевания. Обычно плиты данного типа используют при создании полов.
Характерные особенности ксилолита:
- Негорючесть
- Высокий уровень прочности на сжатие (5-50 МПа, зависит от вида материала)
- Стойкость к ударным нагрузкам, отсутствие риска смятия, сколов
- Отличные тепло/шумоизоляционные характеристики
- Стойкость ко влаге, морозу
Изготовление блоков своими руками
Приступая к созданию блоков из опилок и цемента своими руками, необходимо хорошо изучить весь процесс и учесть нюансы.
Как создать блоки самостоятельно:
- Подготовить все инструменты для работы со смесью и устройства – бетономешалка, молотковая дробилка, рубильная машина, вибропрессовальная машина, вибростанок и т.д.
- Подготовить сырье – купить в строительном магазине цемент М400 минимум, заказать чистый песок, известь (можно глину), найти на заводе много древесных опилок (желательно сухих, если регион влажный – нужно также запастись минерализаторами для обработки опилок, в качестве которых могут выступить жидкое стекло или известковое молоко).
- Тщательное измельчение древесины путем загрузки в рубильную машину, а потом в молотковую дробилку (для получения одинаковой фракции).
- Аккуратный просев щепы, чтобы отделить мусор, землю, кору и т.д.
- Пропитка щепы – вымачивание в смеси жидкого стекла с водой в пропорции 1:7. Для ускорения прохождения процесса минерализации и затвердевания материала можно добавить немного хлористого кальция.
- Обработка гашенной известью – дезинфекция от вредителей.
- Смешивание – для получения стандартной смеси берут 1 тонну портландцемента, 250 кг извести и 2.5 тонн песка. Объем щепы определяется отдельно, исходя из нужных характеристик и вида блоков. Все смешивается в бетономешалке.
- Заливка смеси в формы, установка на вибропрессовальный аппарат.
- Сушка – натяжение пленки на емкость с формами, выдержка в помещении 12 суток при температуре +15 градусов и выше (в холоде гидратация будет проходить медленнее гораздо). Периодически материал можно проверять – если сухо, увлажнять водой.
Блоки из опилок и цемента – прекрасный выбор для выполнения множества работ в сфере ремонта и строительства малоэтажных зданий. При правильном выборе качественного материала и соблюдении технологии работы, создании оптимальных условий опилкобетон обеспечит надежность, прочность и долговечность конструкции.